When it comes to automobile design, body structure and construction methods play a crucial role in defining a vehicle’s safety, performance, and efficiency. Over the years, manufacturers have developed a range of body structures to meet varying needs, from lightweight materials to enhance fuel efficiency to reinforced frames for improved safety. These construction methods can be broadly categorized into unibody, body-on-frame, and spaceframe designs, each offering unique advantages for different types of vehicles, from sedans and SUVs to sports cars and heavy-duty trucks. Understanding these methods helps drivers appreciate the engineering behind their ride.
Ladder Frame
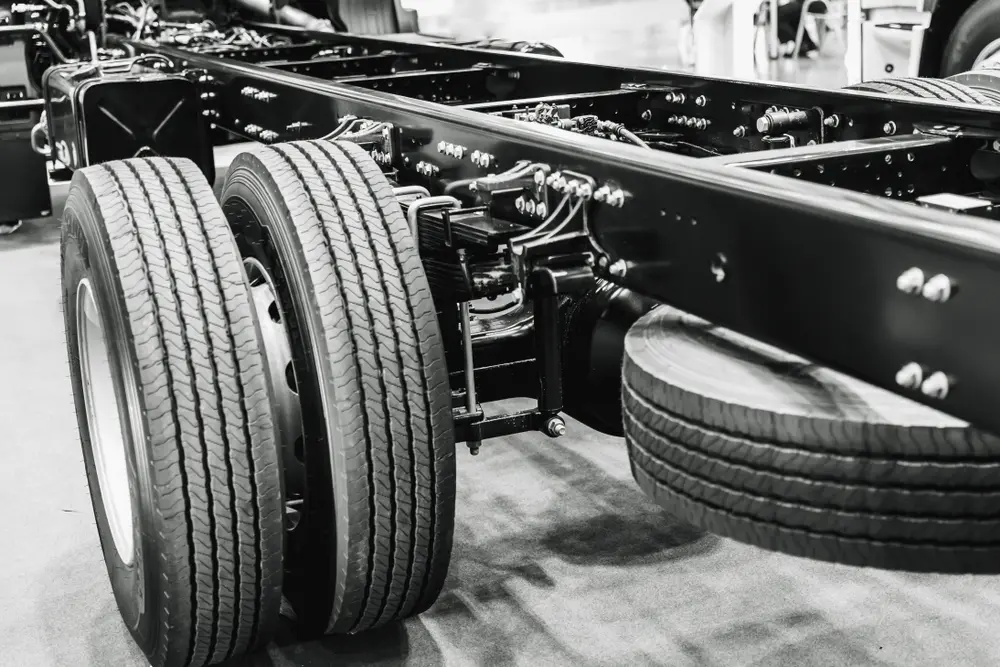
The earliest and most basic form of automotive structure is the ladder frame, where structural members are joined at right angles to form a strong and simple frame. Usually this is in the form of two main members running the length of the vehicle, strengthened by transverse crossmembers and outriggers to support the body, drivetrain and running gear. This gives the bare frame the appearance of a ladder, hence the name.
The ladder frame is simple to construct, rugged, easy to repair and makes for a versatile platform since any bodywork serves no structural purpose. Its disadvantages are its weight (which can only be reduced at the expense of strength and rigidity), the high centre of gravity it imposes on the vehicle, the restricted interior space caused by the need to accommodate the bulky frame structure and poor refinement.
Once near universal for all motor vehicles, the ladder frame is today found only on heavy-duty commercial vehicles, pick-up trucks, off-roaders and other specialist applications where strength and simplicity take priority.
The strongest form of ladder frame uses welded lengths of steel box section. Weight can be reduced without sacrificing too much strength by using C- or U-section steel instead.
Perimeter Frame
The perimeter frame became the traditional way passenger cars were built in the USA for several decades from the 1950s. Instead of the main frame members running straight under the body, with the perimeter frame they ran outwards under the body door sills.
This allowed gains in space and a lower ride height while adding side impact protection. Because this design required little to no structural strength in the bodywork and left a large amount of free space between the wheels, it made it cost-effective to offer different car models on the same frame and change the bodywork each year, as became common in the American car industry to increase sales. The last traditional American sedan on a platform frame was the Ford Crown Victoria, sold until 2012.
Spine Frame
Originally developed for lightweight economy cars in the inter-war period, and then used for sports and racing cars from the 1950s onwards, the spine frame is like an extreme version of the X-frame. The main strength of the vehicle is in a single large tubular or box section which holds the mechanical parts, with the body attaching at each and to side members which usually have no other structural purpose. The spine frame is light and strong, but has poor interior space, refinement and crash safety, making it preferred only for specialist vehicle designs.
Spaceframe
The spaceframe consists of a three-dimensional ‘skeleton’ of steel or aluminium tubes. For maximum rigidity and strength, they are arranged to form triangles, like a more complex version of a bike frame. Spaceframes are light, strong and simple to make so ideal for low-volume, lightweight and specialist vehicles. It is expensive to produce in volume and requires exotic materials like carbon fibre and sophisticated design methods to meet the safety standards of a mass-production car.
Monocoque
In true monocoque construction, the skin and the structure are one and the same (like an eggshell). This is very rare in automotive design due to the cost of construction and the practical disadvantages it brings. Most true monocoque cars are single-seater racing cars (such as those in Formula One or IndyCar) or specialist sports cars. Monocoque construction is especially suited to exotic materials such as aluminium alloy or carbon fibre.
Unibody
By the far the most common type of structure on modern automobiles is the unibody, which combines features of the platform frame and the monocoque to produce a design that is light, strong and easy and cost-effective to mass produce. By eliminating the frame and using the same basic principles of a monocoque, a unibody car will be lighter, with better rigidity and a lower centre of gravity. The first unibody (or ‘unitary construction’) cars were made in the 1930s and they increased in popularity from the 1940s to the 1970s. By the 2000s virtually all mass-produced road cars used unibody construction.
Unibody cars have a welded structure forming the floor, transmission tunnel, sills/rocker panels, firewall, door frames, engine compartment roof and rear bodywork into a single structural component. External body panels and movable panels (hood, doors, trunk lid) bolt on. Most of the strength is in the floor, rockers and firewall. Most cars still use steel for unibodies, but examples exist of using aluminium alloy and carbon fibre for some or all the sections.
Mixed Construction
In some cases, vehicles use elements of multiple methods of construction. For instance, some Sports Utility Vehicles combine traditional ladder or perimeter frame with a unibody passenger compartment – the frame provides strength and carries the drivetrain and running gear loads, while the unibody provides good refinement, space and crash safety. The disadvantage of this approach is excess weight and additional cost. Similarly, a lot of sports cars have a monocoque for their passenger compartment (often called a ‘tub’) and a spine frame, or the front half of a ladder frame, to carry the drivetrain.
Also Read- Live Dealer Games vs Game Shows: Which One’s Right for You?